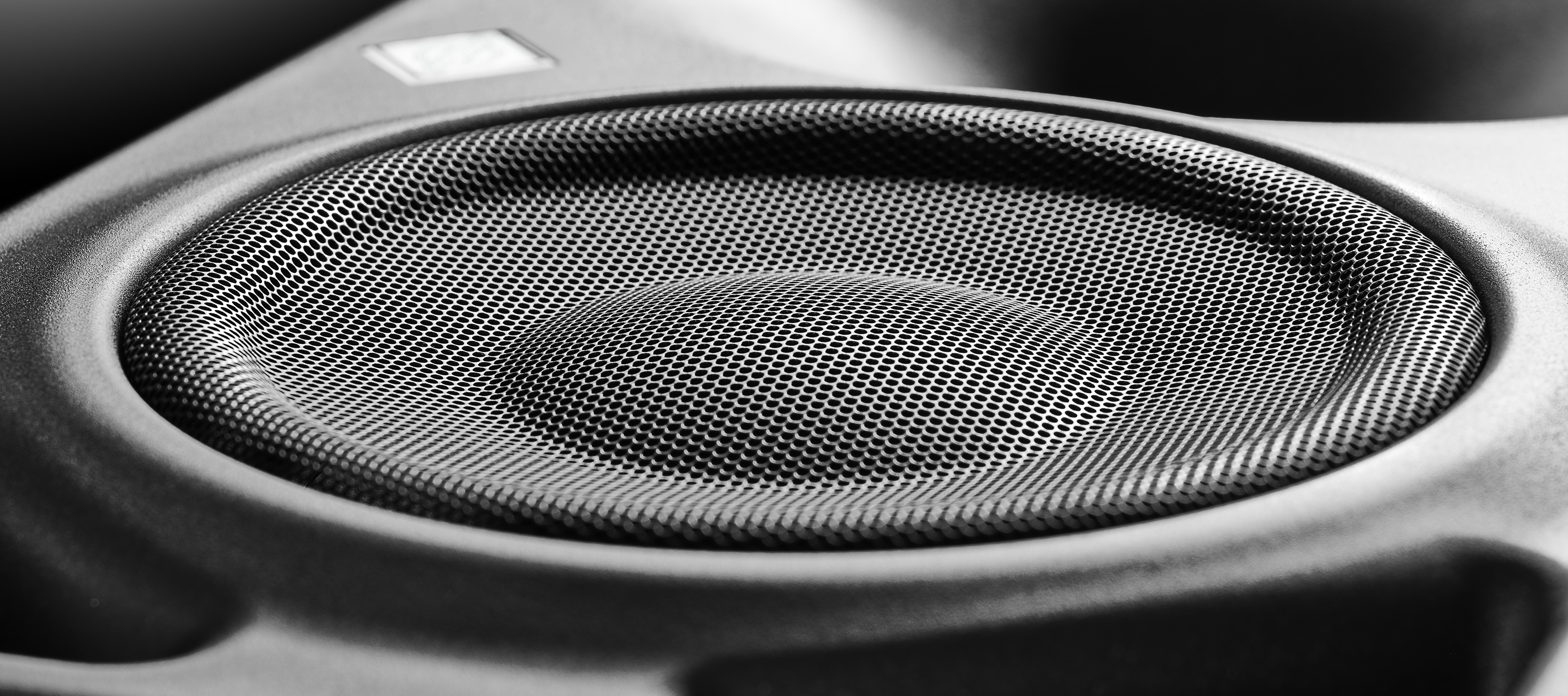
In an audio system, the woofer is responsible for reproducing the most impactful low-frequency sound, whether it's a drum beat in music or a shocking explosion in a film, a quality woofer is indispensable. However, the sound quality of a woofer is not only determined by its shape or power, but also by the materials it is made of. In this article, we'll look at some of the key components and analyse how materials affect the sound quality of a woofer.
Voice Coil Materials
The voice coil is the heart of the diaphragm movement, for the woofer, the power carried is often larger, the current required is strong, the heat is also more serious. Therefore, voice coil materials must have excellent conductivity and high temperature resistance. Common voice coil materials include copper, aluminium, and its matching sonic skeleton materials, such as polyimide (PI), glass fibre (GSV), Nomex and so on.
For example, the use of copper wire wrapped around a glass fibre skeleton of the sonic skeleton can not only withstand higher power, but also maintain structural stability over a long period of time, avoiding distortion or even damage due to high temperatures. The difference in materials directly determines the durability of the speaker and the linear output of the sound.
Magnet Material
The role of magnets is to provide a magnetic field for the voice coil, thus generating a driving force to push the diaphragm. Woofers have high magnetic requirements, so the choice of magnet is especially critical. Ferrite magnets are widely used in low-end and mid-range woofers because of their low cost and good stability. In contrast, NdFeB magnets have a higher flux density and lighter weight, providing a stronger dynamic response, and are commonly used in high-end professional audio equipment.
The larger the magnet, the better the performance, the stronger the performance of the speaker in the large dynamic, low-frequency dive and so on. However, this also means an increase in manufacturing costs, requiring sophisticated thermal management and structural design to match.
In addition, the magnetic properties of magnets made of different materials can subtly affect the tonal performance of a speaker, which is one of the important factors that high-end audio manufacturers need to consider when tuning.
Cone Structure
Woofers are large and magnet-heavy, so if the cone structure isn't strong enough, it's prone to resonance or deformation, which can affect the purity of the sound. High-end woofers often use die-cast aluminium cone frames, which not only have high strength, but also effectively suppress cabinet resonance. Low-end products often use stamped steel cone frames, which are lower in cost but less stable under high power.
A sturdy cone frame structure, not only can enhance the clarity of the sound, but also extend the service life of the speaker.
Diaphragm Material
Diaphragm is the electrical signal into sound fluctuations in the core components, its material properties directly affect the sound of the timbre, response speed and the degree of distortion. Common diaphragm materials include coated paper cone, polypropylene (PP), aluminium alloy, carbon fibre and so on.
For example, coated paper cones have certain damping characteristics while ensuring good rigidity, making low frequencies more natural and thick; aluminium alloy diaphragms are more rigid and suitable for fast, clean bass output; and composite materials such as carbon fibre are both lightweight and strong, and are able to maintain good deformation control under high-power propulsion to improve overall sound quality.
Surround and Spider
Suspension systems consist mainly of the surround and the spider, which control the maximum displacement and rebound of the diaphragm. Soft foam or rubber surround provide greater linear displacement, which is essential for good low frequency performance. Spiders are usually made of phenolic or coated cotton fabrics, which are strong and heat-resistant, and can withstand long periods of high amplitude operation.
A good suspension system improves the transient response of the woofer, making the sound tighter and firmer, and avoiding trailing and ‘bottoming out’ problems.
Dust Caps and Grille
Although Dust Cap and Grille may seem like accessory items, they also have a subtle effect on the sound. A rigid dust cap reinforces the overall rigidity of the cone and aids in extending the high frequency response, while a grille is needed to avoid blocking the reflection holes or creating airflow noise to ensure a pure low frequency output.
Cabinet Structure
The last, and most relied upon part of the woofer is the cabinet construction. Closed cabinets are good for tight, powerful bass output, while bass-reflexes (with pilot holes) enhance the low-frequency dive and boost the sense of energy. The materials used in the cabinet, such as MDF, plywood or engineering plastics, need to have good airtightness and internal damping properties to control standing waves and cabinet resonance.
Each component of the woofer, from the voice coil and magnet to the diaphragm and cone, and even the seemingly insignificant surround and cabinet structure, is shaped by the material properties of each to create the final sound performance. In other words, the sound quality of a woofer is not only the result of stacked technology, but also a perfect combination of material science and acoustic engineering.
For the average user, understanding the difference between these materials can help make more informed purchasing decisions; while for sound designers, a reasonable combination of materials is the key to creating quality bass.